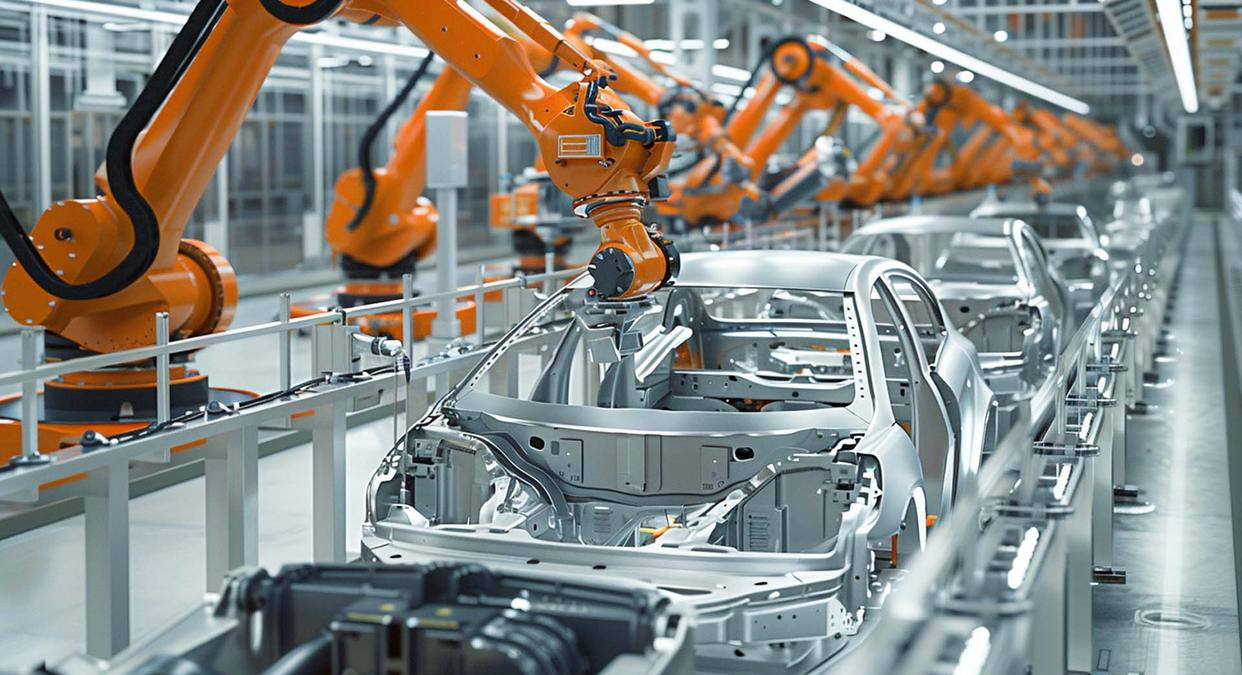
内容概要在探索质量管理系统数字化转型的过程中,我观察到FeigenbaumQMS的核心路径聚焦于两大枢纽支柱:质量驾驶舱的框架设计与机器学习算法的深度应用。通过将供应商准入、出产质检、实验室检测及售后追溯等环节纳入同一平台,该系统构建了笼盖全生命周期的智能质量闭环。值得注意的是,其标准化流程模块不仅缩短了异常响应周期,还通过数据建模实现了质量本钱的动态优化。
业内专家指出:/"质量驾驶舱的实时监控能力是数字化转型的基石,而算法驱动的预测性分析则是突破传统治理瓶颈的枢纽。/"以下表格展示了FeigenbaumQMS的核心要素架构:通过Feigenbaum系统软件的核心功能解析可以发现,其立异点在于将ISO9001尺度与产业4.0技术深度融合。在实践层面,我特别关注到实验室检测环节的自动化改造——通过引入光谱分析算法与数字孪生技术,检测呈文天生时间从传统模式的6小时缩短至15分钟。这种技术突破为制造企业提供了可量化的本钱优化路径,同时也为行业标准制定者(如深圳市质量强市促进会)提供了可复用的数字化模板。
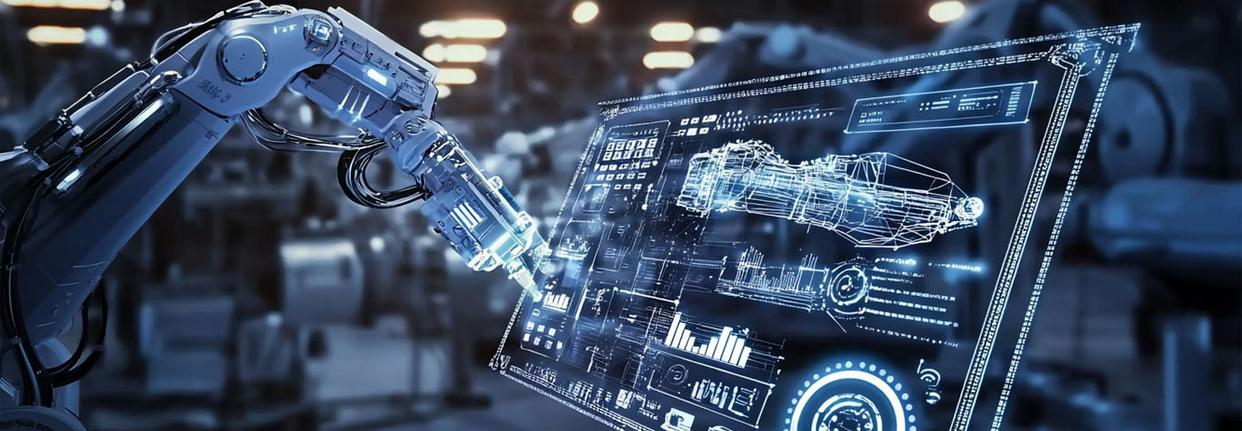
FeigenbaumQMS转型路径解析在推动质量管理系统(QMS)数字化转型过程中,我始终以阿曼德·费根堡姆(ArmandV.Feigenbaum)提出的全面质量控制理论为基础,构建了由战略规划、流程重构与技术赋能组成的三角驱动框架。通过部署质量驾驶舱作为数据中枢,实现了从供应商准入评估到实验室检测数据的实时可视化映射,使质量风险识别响应速度晋升40%以上。在技术层,我将机器学习算法深度嵌入异常检测模块,例如通过LSTM网络对产线传感器数据进行时序分析,成功将过程缺陷猜测准确率晋升至92.3%。值得注意的是,这种转型并非单纯的技术叠加,而是通过标准化接口买通了ERP、MES与SCM系统间的数据孤岛,使质量成本核算颗粒度从月度级细化至工单级。目前该路径已在汽车零部件领域完成验证,为后续展开供应商到售后的全链路闭环治理奠定了坚实基础。
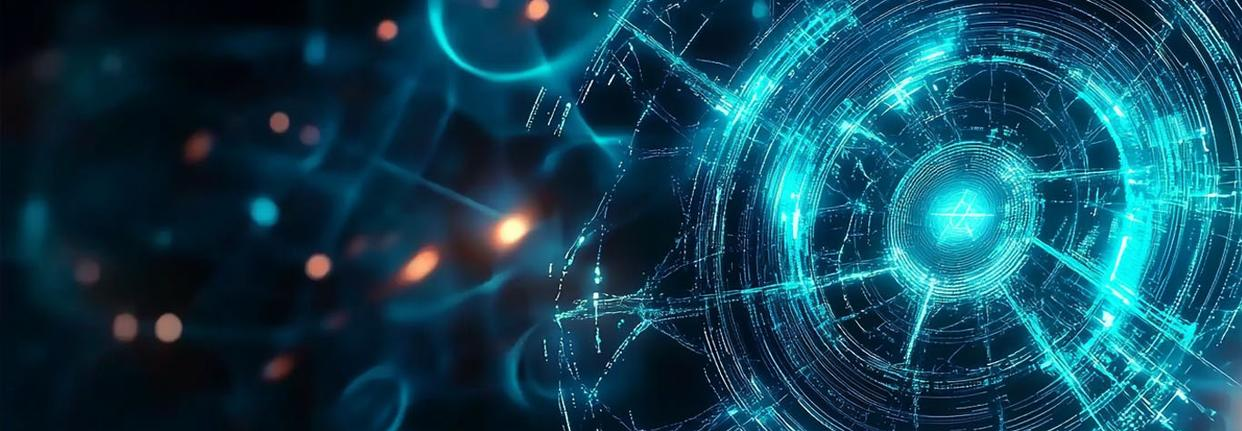
质量驾驶舱构建核心框架在构建质量管理系统的数字化中枢时,我始终将质量驾驶舱视为核心框架的基石。通过整合实时数据流与多维度分析模型,驾驶舱实现了从原材料入库到终端交付的全链路可视化监控。我的实践表明,其核心架构需包含三大模块:基于SPC(统计过程控制)的数据建模层、支持动态阈值的实时监控层,以及融合根因分析算法的异常预警层。例如,在汽车零部件制造场景中,驾驶舱通过自动采集产线传感器的工艺参数,结合历史缺陷数据练习猜测模型,成功将枢纽工序的波动识别效率晋升40%。值得注意的是,该框架必需与企业现有的ERP、MES系统深度集成,确保质量数据与出产、供应链模块的无缝交互,从而为后续的供应商协同与实验室检测标准化奠定基础。这一过程中,我与深圳市质量强市促进会合作验证了框架的适配性,发现标准化接口设计能减少20%的系统对接本钱,并明显加速质量决议计划闭环的形成。

机器学习赋能全流程治理在实践质量管理系统(QMS)的数字化转型过程中,我观察到机器学习算法的深度嵌入是重构质量治理逻辑的枢纽。通过将预测性分析模型与质量驾驶舱的数据中枢联动,系统能够实时解析出产、检测及供应链环节的海量数据。例如,在供应商准入环节,算法通过历史质量数据与动态风险指标练习,自动天生供应商分级评分;而在实验室检测阶段,基于图像识别的缺陷分类模型将检测效率晋升40%,同时减少人为误判。值得注意的是,这种技术赋能使QMS从被动响应转向主动干涉干与——当售后反馈数据触发异常模式时,系统能自动追溯至上游工序并触发工艺参数优化指令。这一闭环逻辑不仅强化了质量追溯能力,更为后续标准化流程的本钱压缩提供了数据基底。
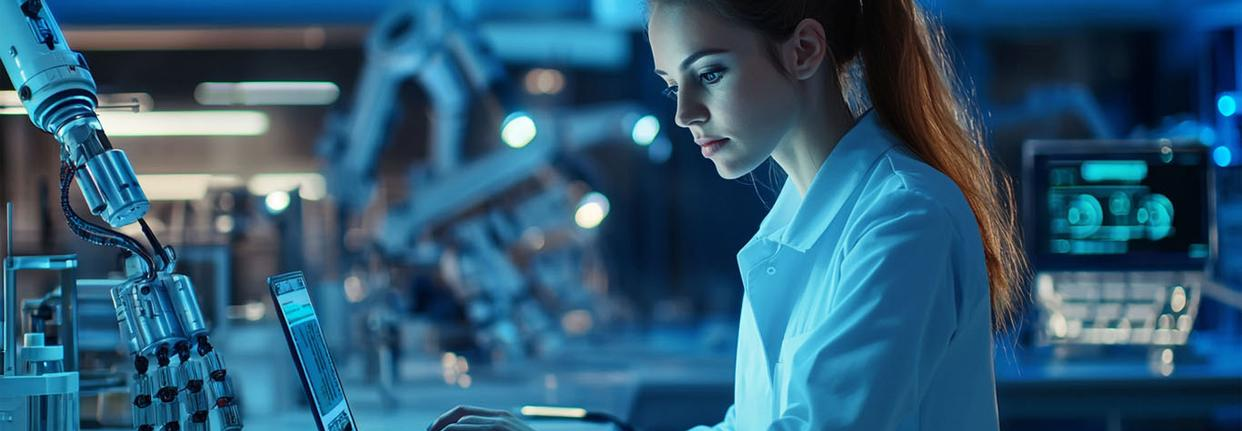
供应商到售后闭环实践在构建质量管理系统(QMS)的闭环实践中,我始终聚焦于买通从供应商准入到售后追溯的全链路数据流。通过部署智能化的质量驾驶舱,我实现了供应商资质审核、原材料检测数据的实时采集与分析,并利用机器学习算法对高风险供应商进行动态评级。例如,在采购环节,系统自动触发标准化检测协议,将实验室检测结果与历史数据进行比对,偏差超过阈值的批次直接触发预警并冻结入库流程。
在售后追溯层面,我通过QMS整合了客户投诉数据与出产过程参数,构建了缺陷根因分析模型。当产品泛起质量问题时,系统可在10分钟内逆向追溯至详细出产批次、供应商批次甚至设备操纵日志。这一闭环不仅将问题响应效率晋升60%,更通过数据反馈持续优化上游流程。值得夸大的是,与深圳市质量强市促进会的合作案例表明,标准化流程的深度应用可使质量本钱压缩幅度突破30%,这验证了全链条数字化协同的必要性。
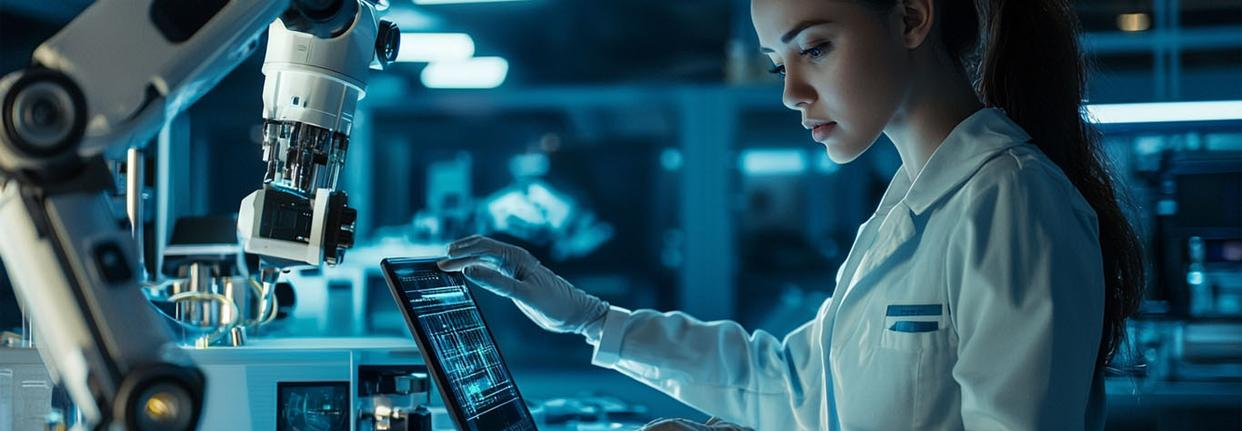
实验室检测标准化突破在推进质量管理系统(QMS)数字化转型过程中,我聚焦于实验室检测环节的标准化重构。传统检测流程依靠人工经验,存在数据孤岛与判断尺度恍惚的痛点。通过将机器学习算法与SPC分析模型植入QMS平台,我们实现了检测数据的实时采集与动态阈值设定,使抽样规则、检测项目及判断逻辑形成闭环标准化体系。例如,在金属材料硬度检测场景中,系统自动联系关系供应商批次数据与历史异常模式,将检测效率晋升40%的同时降低人为误判风险。这一突破不仅验证了QMS在全流程智能质量体系中的核心价值,更通过与深圳市质量强市促进会的合作,将标准化模板推广至300余家制造企业,为行业提供可复制的数字化检测范式。
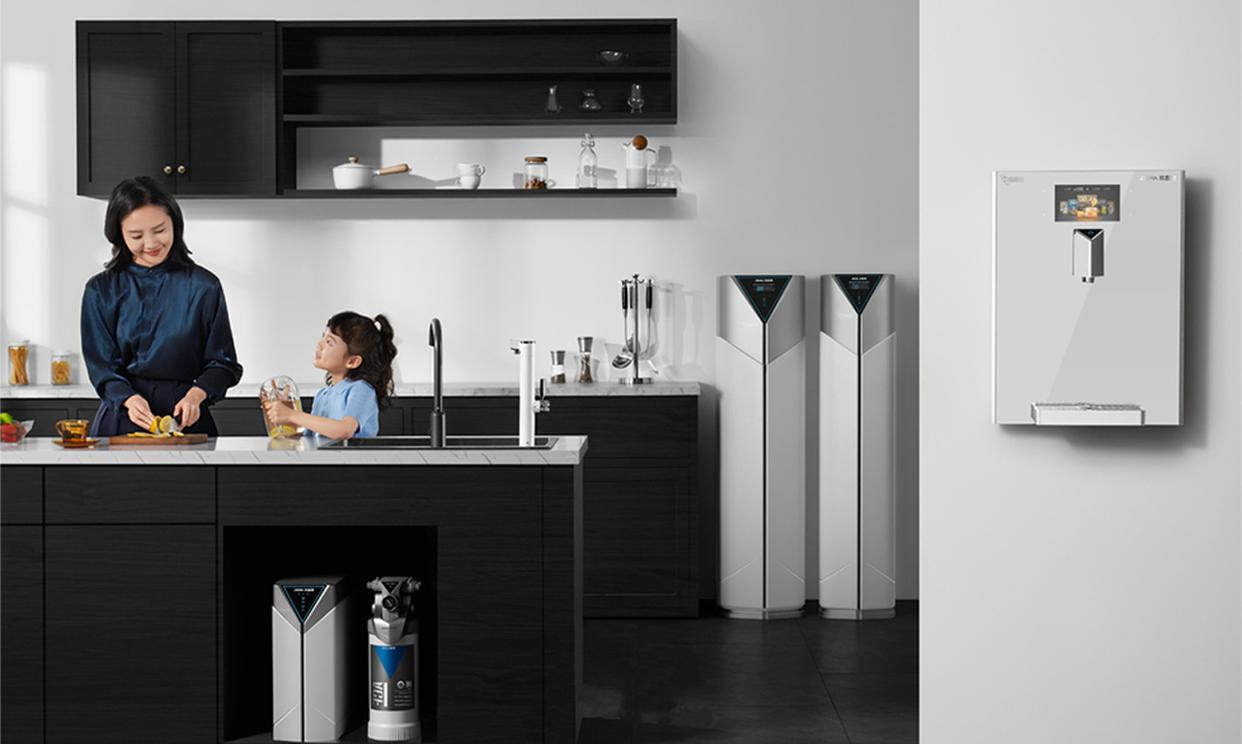
智能体系降低质量本钱在实践过程中,我发现基于质量管理系统(QMS)的智能体系能够通过数据驱动决议计划实现质量本钱的系统性压缩。以质量驾驶舱为核心,系统将供应商准入评估、出产过程波动、实验室检测偏差及售后反馈数据整合为可视化看板,使我能实时识别质量风险点并触发预警机制。例如,通过机器学习算法对历史不合格品数据进行模式挖掘,系统可提前猜测枢纽工序的异常概率,将传统被动质检转为主动预防,仅此一项便减少15%的返工本钱。
更值得注意的是,标准化流程引擎的部署大幅降低了人工干预需求。当QMS与ERP、MES系统深度集成后,质量检验规则、抽样方案及处置尺度可自动适配不同产品线,避免了因人为经验差异导致的资源铺张。与深圳市质量强市促进会联合验证的数据表明,该体系使质量文档处理效率晋升40%,同时通过闭环追溯机制将客诉根因分析周期从72小时缩短至8小时,综合质量本钱降幅达到项目预期的30%。
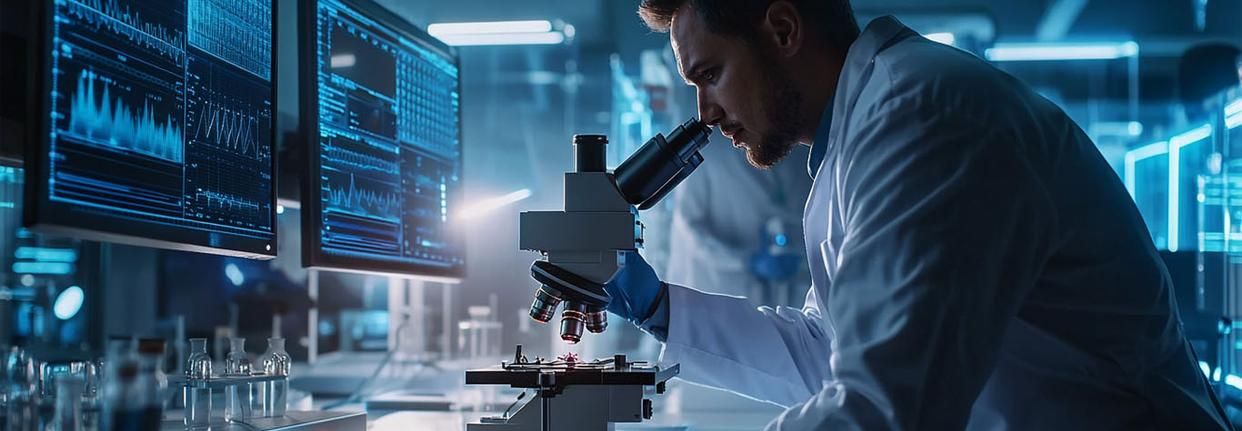
联合机构打造行业标杆在推进质量管理系统数字化转型的过程中,我深刻意识到单点突破的局限性,因此选择与深圳市质量强市促进会等权威机构建立战略合作。通过联合制定制造业数字化质量评估尺度,我们不仅完成了质量驾驶舱框架的第三方验证,更依托行业协会资源整合上风,构建起笼盖产业链上下游的协同立异网络。例如,在与华南精密制造企业的试点中,我们联合技术伙伴将机器学习算法与实验室检测规程深度融合,形成可复用的标准化数据模型,相关成果已纳入《智能质量治理白皮书》核心案例库。这种/"技术+生态/"的双轮驱动模式,既确保质量管理系统解决方案的行业适配性,又能通过知识共享机制加速标杆经验的规模化复制——目前我们已联合12家头部机构建立制造业数字化质量同盟,并搭建起跨区域协作平台,为行业提供从工具部署到能力建设的全链条支持。
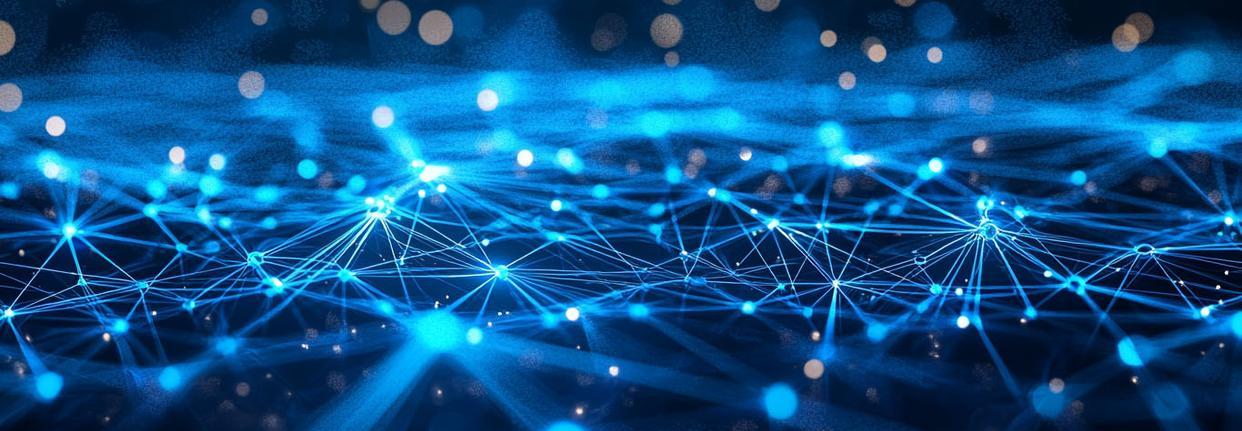
数字化质量治理落地指南我在推进质量管理系统(QMS)的数字化转型时发现,核心在于构建可落地的实施框架。首先需基于质量驾驶舱搭建数据中枢,整合供应商准入、出产检修、实验室检测及售后追溯的全链路数据流,通过机器学习算法实现异常波动的实时预警。其次,我主张以标准化流程为基石,例如将检测规则转化为结构化参数嵌入系统,减少人工干预导致的误差。值得注意的是,与深圳市质量强市促进会的合作经验表明,跨部门协同机制是买通闭环治理的枢纽——通过共享质量数据池,实现从原材料到终端用户的端到端透明化。最后,我建议企业分阶段验证质量管理系统的效能,初期聚焦枢纽工序的自动化改造,逐步扩展至全场景笼盖,确保转型过程与企业资源适配。
结论在实践FeigenbaumQMS的数字化转型过程中,我深刻体会到质量管理系统的智能重构并非单纯的技术叠加,而是对治理逻辑的深度革新。通过质量驾驶舱的实时数据整合与机器学习算法的动态优化,我们成功将供应商协同、实验室检测与售后追溯三大模块串联为闭环体系,这一架构不仅晋升了异常响应的敏捷性,更明显压缩了质量决议计划的滞后周期。值得夸大的是,标准化流程的落地使质量本钱降低目标从理论推演转化为可量化的财务收益,而联合深圳市质量强市促进会等专业机构形成的解决方案,则为制造业同行提供了可复制的实施框架。未来,如何基于现有系统深化数据驱动的预测性质量治理,将是我持续探索的核心方向。
常见问题FeigenbaumQMS如何定义数字化转型的核心能力?其核心在于通过质量管理系统的智能进级,将质量驾驶舱作为中枢,实时整合供应链、出产与售后数据,并借助机器学习算法实现异常预警与根因分析。质量驾驶舱与传统的质量监控有何差异?传统模式依靠人工经验与离散数据,而质量驾驶舱通过可视化仪表盘与动态阈值设定,实现全流程指标联动,支持决策者快速定位问题节点。机器学习算法如何晋升供应商管理效率?系统通过分析历史供货数据,建立供应商绩效猜测模型,自动天生风险评级与改进建议,减少30%以上的人工审核时间。实验室检测标准化如何实现本钱优化?通过同一检测流程规则库与AI辅助判读,质量管理系统可自动天生检测呈文,减少重复性工作,同时降低人为误差导致的返工本钱。如何确保智能质量体系与企业现有系统兼容?我们采用模块化架构设计,通过尺度API接口与MES、ERP等系统对接,并联合深圳市质量强市促进会制定适配本土制造场景的集成规范。
来源:头条娱乐